(1) helix angle β helix angle is the angle between the outermost spiral line on the spiral groove of the drill bit and the drill bit axis after being expanded into a straight line. Since the lead of each point on the spiral groove is the same, the helix angle at different diameters of the drill bit is different. The helix angle at the outer diameter is the largest, and the closer to the center, the smaller the helix angle is. When the helix angle is increased, the rake angle increases, which is beneficial to chip removal, but the rigidity of the drill bit decreases. The spiral angle of standard twist drill is 18 ° ~ 38 °. For drill bits with smaller diameter, the spiral angle should be taken as a smaller value to ensure the rigidity of the drill bit.
(2) rake angle γ Om [because the rake face of twist drill is fusilli, the rake angle of each point on the main cutting edge is different. From the outer circle to the center, the front corner gradually decreases. The front angle at Tool nose is about 30 °, and it is about-30 ° near the transverse edge.
Horizontal blade the upper front angle is-50 ° ~-60 °.
(3) rear angle α Om [twist drill the rear angle of the selected point on the main cutting edge is expressed by the feed rear angle α Om in the section of the point column. The column section is a cylindrical surface formed by passing through the selected point m of the main cutting edge as a straight line parallel to the axis of the drill bit, which rotates around the axis of the drill bit. Along the main cutting edge, α Om also changes, and the closer to the center, the larger α Om. Twist drill the back angle α at the outer circle, usually 8 ° ~ 10 °, and 20 ° ~ 25 ° at the back angle at the transverse edge. This can make up for the influence caused by the reduction of the actual working back angle of each point on the main cutting edge due to the axial feed movement of the drill bit, and can adapt to the change of front angle.
(4) tool cutting edge angle Kappa rm tool cutting edge angle is the angle between the tangent projection of the selected point m of the main cutting edge on the base surface and direction of feed. The base surface of twist drill is the plane containing the drill axis through the selected point of the main cutting edge. Since the main cutting edge of the drill does not pass axial lead, the base surface of each point on the main cutting edge is different, and the tool cutting edge angle of each point is also different. When the vertex angle is worn out, the tool cutting edge angle of each point is determined accordingly. Tool cutting edge angle and vertex angle are two different concepts.
(5) front angle 2φ front angle is the included angle of two main cutting edges projected on their parallel planes. The smaller front angle is easy to cut into the workpiece, and the axial resistance is small, which increases the working length of the cutting edge and reduces the nominal thickness of the cutting layer, which is beneficial to heat dissipation and improves the durability of the cutting tool; if the front angle is too small, the strength of the drill bit decreases, the deformation increases, the torque increases, and the drill bit is easy to break. Therefore, according to the material of the workpiece
strength and hardness to grind reasonable front angle, standard twist drill front angle 2φ is 118 °
(6) the bevel angle of the transverse edge psi the bevel angle of the transverse edge is the angle between the main cutting edge and the transverse edge projected on the plane perpendicular to the axis of the drill bit. When the twist drill back knife surface is ground out, it naturally forms. It can be seen from Fig. 3-5 that if the bevel angle of the transverse blade is increased, the length of the transverse blade and the axial resistance decrease. The bevel angle of the standard twist drill is about 50 ° ~ 55 °.
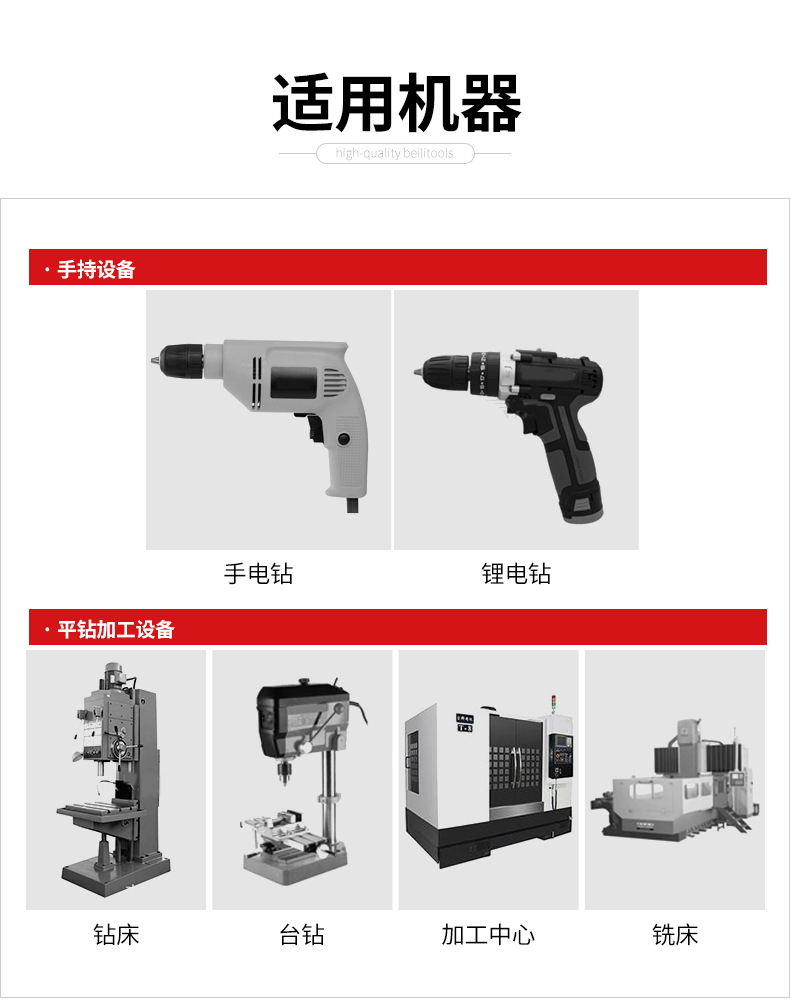
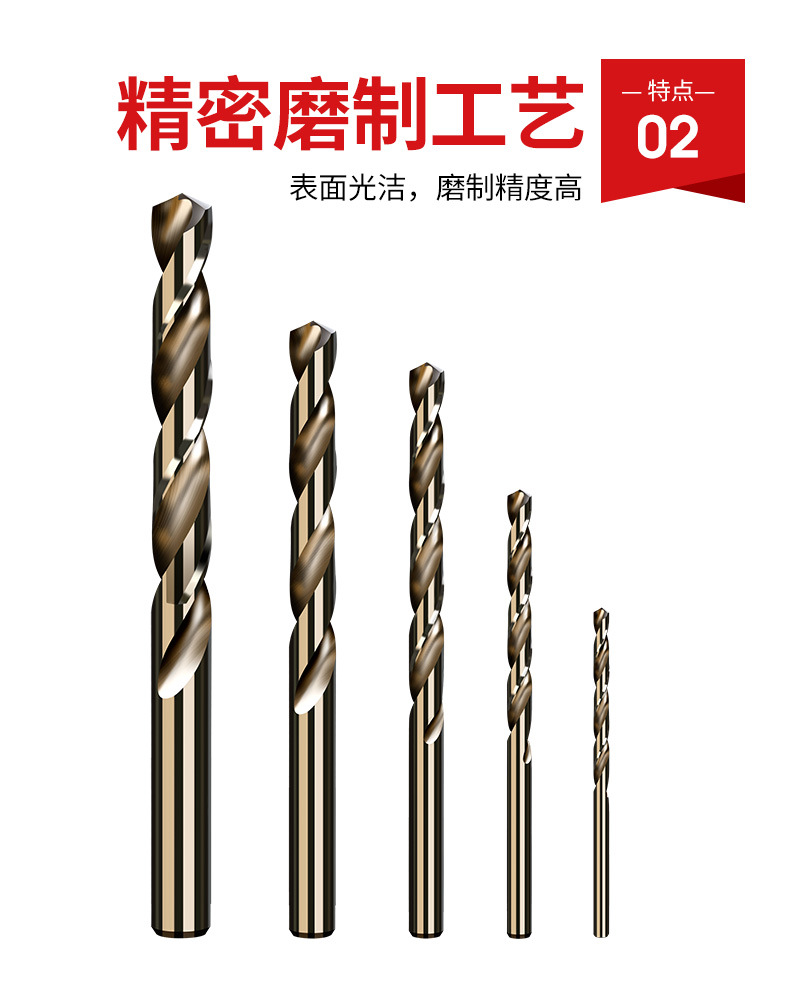
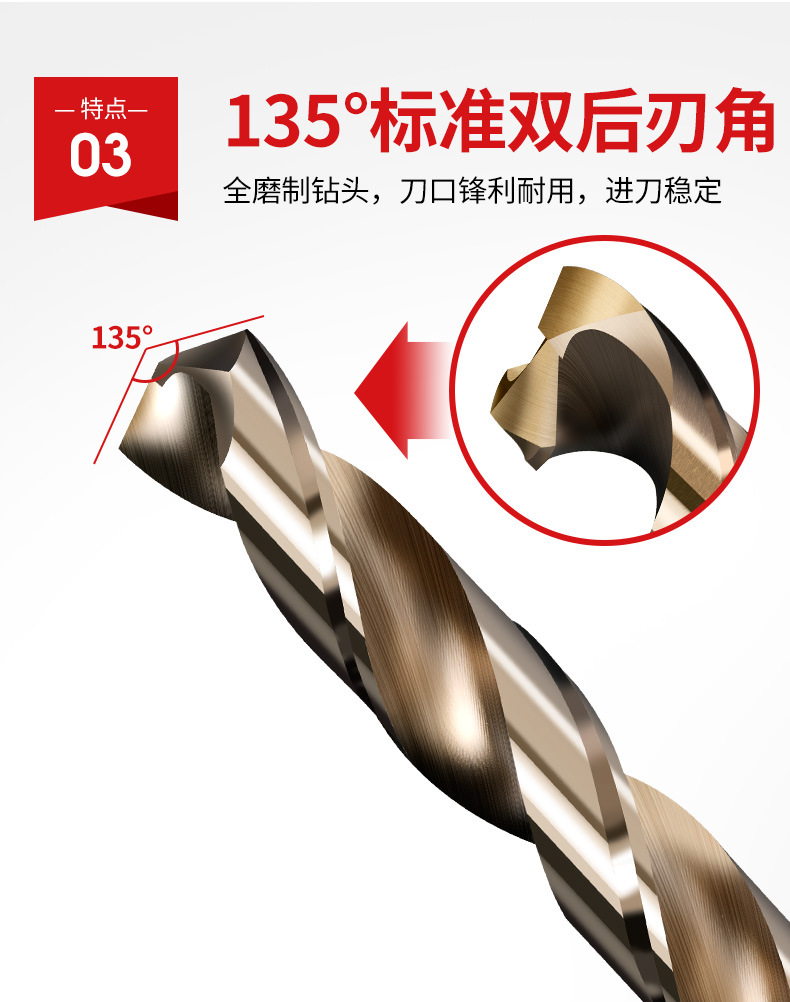
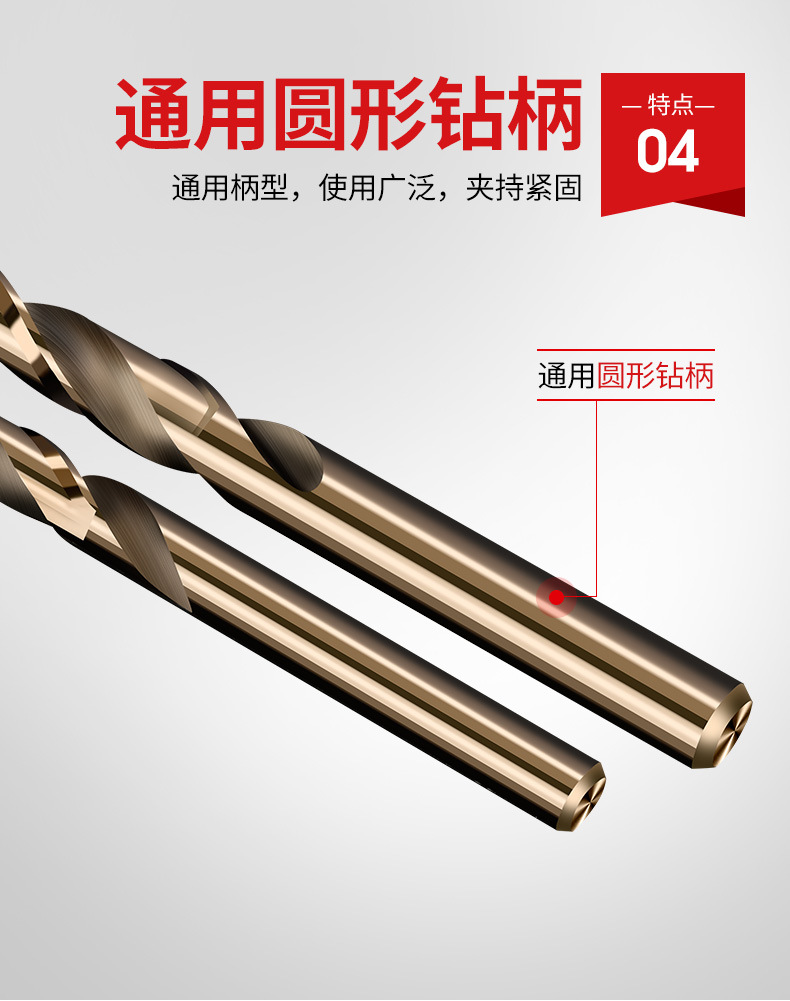
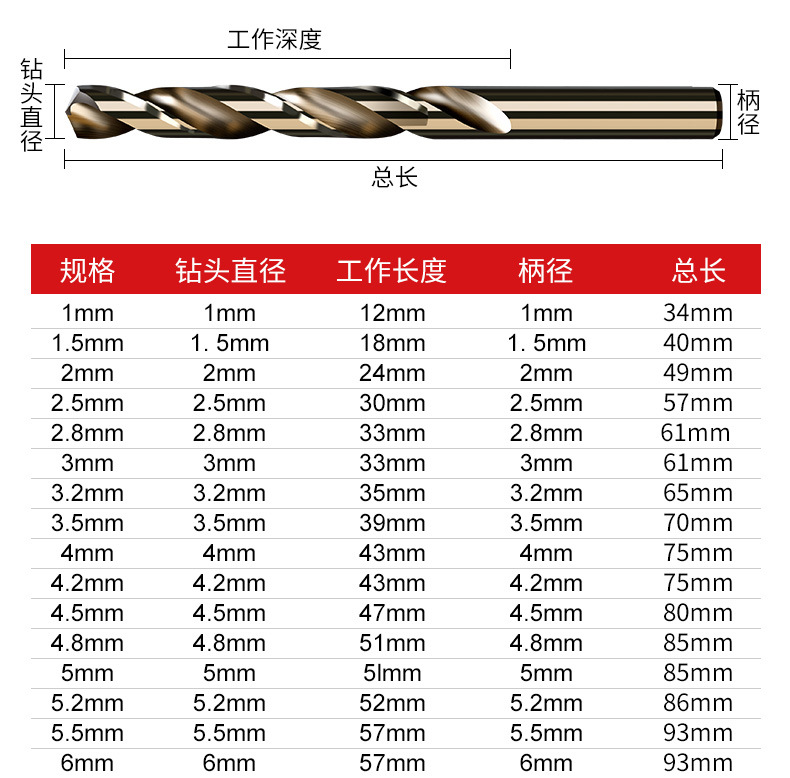